A tailored app optimizing chemical injection in real-time
The Chemical Injection Application (or CIA) is an app that calculates the optimal injection rate of chemicals in different injection points in an oil plant. It has been developed for and with the engineers and operators on the OKEA field Draugen, and has automated and simplified the daily workflow of configuring and calculating optimal injections for different chemicals, reducing risk of injecting too little chemicals, while minimizing excess injection.
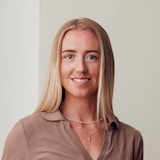
- Author
- Frida Bjørnstad Konow
- Publish date
- · 5 min read
The chemical injection application is one example of a product from our "scalable tailoring" application building framework. The application is currently set up for supporting injection of four different chemicals on Draugen; scale inhibitor, demulsifier, H2S scavenger and biocide. We recently launched the second version of CIA, where it has gotten a significant face lift both front-end and back-end. Further we will dig deeper into the subject of chemical injection with its associated challenges and requirement, and how we have solved it with CIA.

Injection of Chemicals
Typically, the chemicals are injected through different injection points connected to wells, separators and other components in the plant. These injection points can have constraints like maximum injection rate that needs to be taken into consideration. To ensure normal operations in the plant, it is important to ensure a given concentration of chemicals at different points of the oil plant. We refer to the lowest acceptable concentration of a chemical at a given point to a dosage. The problem is then to find which injection points to use and how much chemicals to inject into these injection points to achieve the desired dosages of chemicals at different points in the plant. For a chemical like demulsifier it is the concentration in the separator that matters. Then the engineers only have to define dosages for the separators. The case is more complex for a chemical like scale inhibitor, where the concentration at every “mixing point” is crucial to avoid scaling. Then several dosages should be specified. Looking at the chemical injection from an optimization perspective, it is evident that the problem can be formulated as a optimization problem with the dosages as constraints.
Problem Definition
A simplified optimization problem for any chemical injection in the oil plant can be stated as follows, given some adjustable injection rates, x, and a set of constraints.

Examples of general constraints can be available injection points and maximum and minimum injection rate for each injection point, in addition to the optimal dosages. From an engineer's point of view these constraints should be possible to configure. In addition it should be possible for the engineer to see what impact changes in the constraints have for the optimal solution. This brings us to the goal for the application:
an application where all the constraints are visible and user-defined, which solves the optimization problem automatically and clearly visualizes the results
Solution
We can divide the relevant users into two groups; operators and engineers. Through our thorough user-centered design process, we investigated the need for the two groups. For the operators the most important requirement was to have all chemical data accessible in one view, to be able to quickly get an overview. For the engineers it is important to have a user friendly configuration of the chemicals and be able to see how the chemicals are distributed through the plant. Thus, it was natural to divide the application into different views dedicated to the two user groups.
Solution highlights:
- Intuitive interface respecting the user needs
- Dedicated views for the different users
- Optimal injection calculated using real-time data and operational conditions
Operator View
The operator view has all the necessary information gathered on one page. That includes a display of all active injection points for each chemical with their associated current flows, optimal flows and a recommended adjustment. The different chemicals have separate horizontal modules. Color codes and icons are used to highlight and visualise optimal/suboptimal injections, to draw the attention to the suboptimal points. In addition the tag data is retrieved every 15 seconds and the exact time for the data retrieval is displayed in the dashboard. A screenshot of the operator view with random data is displayed below.

Engineer View
The engineer view is where the constraints for the optimization problem are defined. The set of configurable constraints vary depending on the type of chemical. For scale inhibitor, active injection points and dosages are examples of these configurable constraints. The constraint configurations are gathered in the sidebar of the chemicals tab. In the main page of the chemical tab is a subsea network map. This map visualizes the plant with all its components and connections together with the injection and distribution of the relevant chemical. Concentrations of the chemical are displayed on every connection and colors highlight concentrations that deviate from the optimal. The map also displays all the constraints configured in the sidebar. To see the effect of configuration changes, the engineer can press "Calculate" to solve the optimization problem and the map will be updated with the changes. Once the save button is clicked the new solution of the optimization problem is used for the optimal injections in the operator view. A screenshot of the scale inhibitor view with random data is displayed below.

Based on initial feedback from the users, we have succeed with the goal for the application of a being clear and user-friendly tool to support chemical injection for both operators and engineers. The solution strategy of real-time optimization, ensures that the solution always fulfils the desired constraints. Compared to the previous solution strategy that used a set of logical rules to calculate the optimal injection, optimization is more scalable and robust for corner cases or changes in setup. In addition CIA gives the engineers more insight with the subsea map, that displays all concentrations and how changes affects the injection. In total CIA reduces risk of injecting too little chemicals, while minimizing excess injection.